EVE’s 100Ah prismatic cells are at the forefront of battery technology, especially in terms of their construction and longevity. A key feature that sets these cells apart is their advanced laser welding technology. This blog dives into the specifics of this technology and how it enhances the performance and reliability of these EVE‘s high-capacity cells.
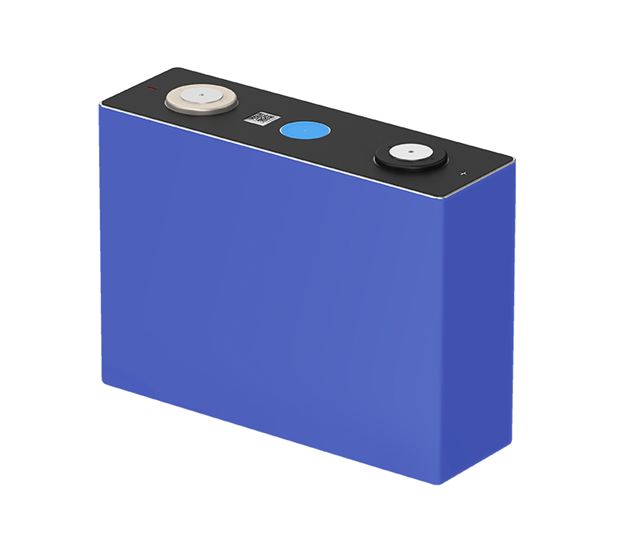
What is a 100Ah Prismatic Cell?
Before we delve into the specifics of laser welding, let’s understand what a 100Ah prismatic cell entails:
– Design: Prismatic cells are flat, rectangular batteries, distinct from cylindrical cells. They are encased in a hard shell which can be either aluminum or a durable composite material.
– Capacity: With a 100Ah capacity, these cells are capable of storing a significant amount of energy, making them ideal for high-demand applications such as electric vehicles, large-scale energy storage systems, and backup power supplies.
The Role of Laser Welding in Prismatic Cells
Laser welding is a sophisticated technique used to join materials using a laser beam. In the context of EVE’s 100Ah prismatic cells, laser welding is employed to achieve several crucial objectives:
Enhanced Precision and Integrity
– Precision: Laser welding provides extremely precise control over the welding process, which is crucial when working with the delicate internal components of a battery. This precision ensures that every weld is consistent, reducing the risk of defects that could impact the battery’s performance or safety.
– Integrity: The bonds formed by laser welding are typically stronger and more uniform than those created through traditional welding methods. This structural integrity is essential for maintaining the robustness of the battery under various operational stresses.
Improved Safety and Reliability
– Safety: By minimizing the heat affected zone (HAZ), laser welding reduces the risk of damaging sensitive components inside the battery. This is particularly important in preventing issues like thermal runaway, a common concern in battery technology.
– Reliability: The robust connections formed by laser welding contribute to the overall reliability of the battery. A well-welded cell is less likely to suffer from internal disconnects or failures, ensuring consistent performance over its lifespan.
Efficiency and Scalability
– Speed: Laser welding is considerably faster than traditional welding methods. This efficiency is vital in scaling up production without compromising on the quality of each cell.
– Energy Efficient: The process is also more energy-efficient, which not only reduces production costs but also aligns with the eco-friendly ethos behind renewable energy technologies.
Why EVE Chooses Laser Welding for Its 100Ah Prismatic Cells
EVE’s decision to employ laser welding technology in the manufacturing of their 100Ah prismatic cells is driven by the need for high performance, durability, and safety. In the competitive landscape of battery technology, these factors are non-negotiable for maintaining industry leadership and customer trust.
Application Benefits
In practical applications, the benefits of laser-welded prismatic cells are clear:
– Electric Vehicles (EVs): EVs benefit from the high energy density and reliability of these cells, translating to longer drive ranges and fewer battery-related issues.
– Energy Storage Systems (ESS): For ESS, the long-term stability and robustness provided by laser welding mean more reliable energy storage solutions, crucial for managing renewable energy sources like solar and wind.
Conclusion
Laser welding technology is a game-changer in the production of EVE’s 100Ah prismatic cells, providing a perfect blend of precision, efficiency, and safety. By integrating this advanced manufacturing technology, EVE not only enhances the performance of its batteries but also sets new standards in the battery manufacturing industry, promising a future where energy storage is more reliable, efficient, and accessible.